Safety
A commitment to excellence
At ATS, safety is paramount. We prioritize the education and training of our employees to ensure a safe and productive work environment.
A key differentiator at ATS is our dedicated Safety Council. This volunteer group actively contributes to enhancing safety protocols by developing Standard Operating Procedures (SOPs), implementing company policies, and designing effective new hire safety programs. The council comprises representatives from all divisions within ATS Welding, ensuring diverse perspectives and employee representation.
Our commitment to safety is further emphasized by our core values, concisely captured in our logo: ALWAYS THINK SAFETY.
Safety services at ATS
With a current Experience Modification Rate (EMR) of .60, safety is a key focus for all our employees. The ATS Safety Department strives to create a safe and healthy work environment through education, communication, and action. Safety at ATS looks like:
- Safety training and education
- Policy development and implementation
- Safety audits and inspections
- Incident investigation and reporting
- Safety communication and awareness
- Safety council operations
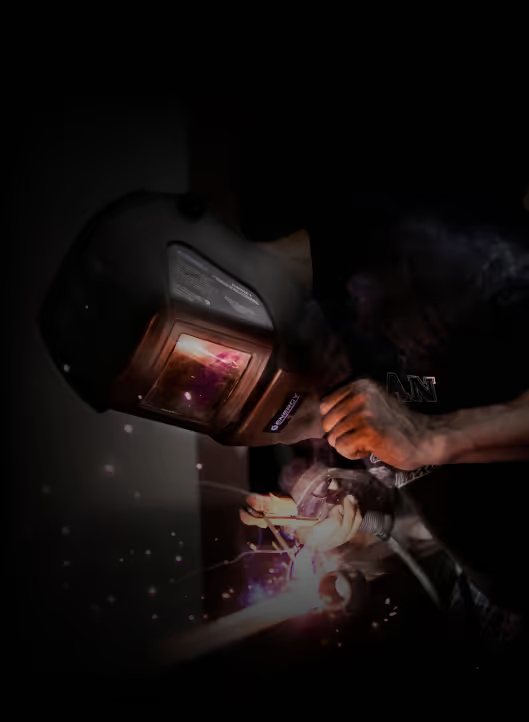
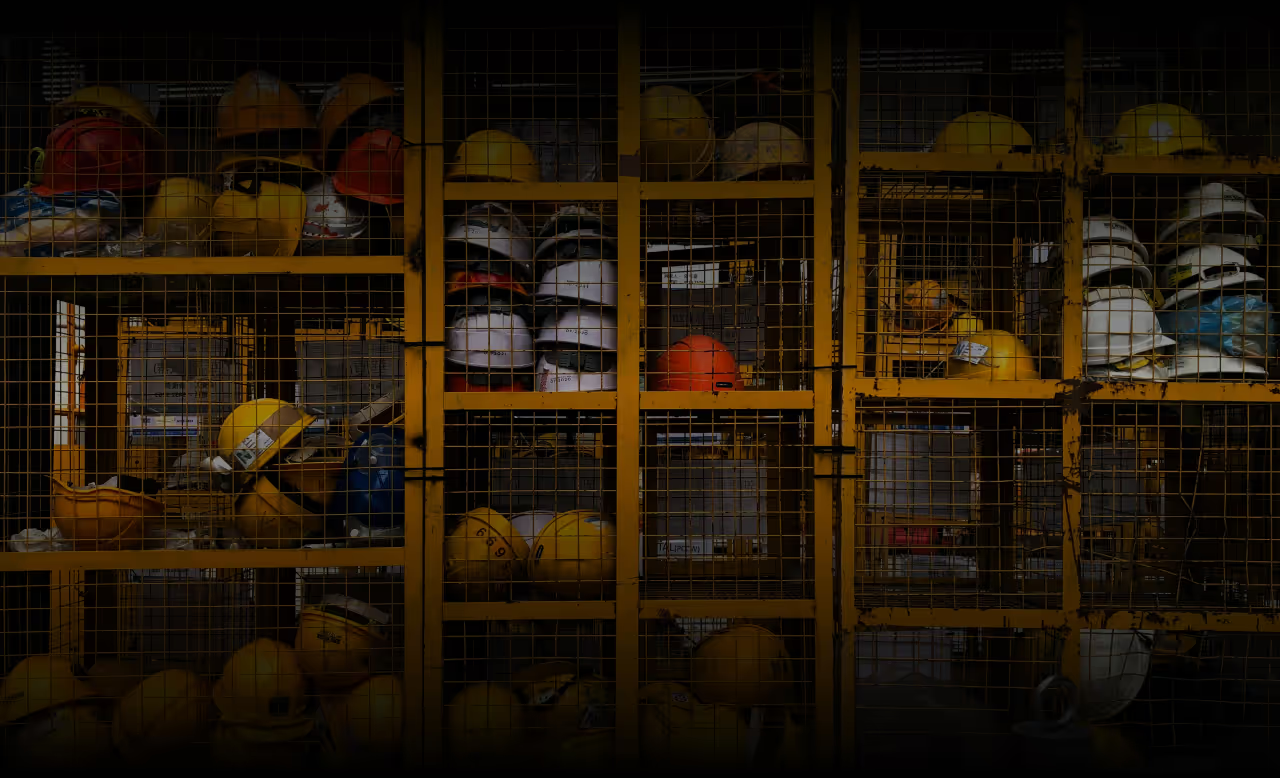